Resin-3D-Druck
So, hier ist nun endlich mal wieder ein neuer Blogpost von uns! Und zwar zu keinem geringeren Thema als 3D-Druck – basierend auf Lennarts Wissen und Erfahrungen. 😉
Wie wir es im Stream angekündigt haben, fassen wir das Verfahren hier nochmal mit Bildmaterial zusammen, damit man sich unter dem Ganzen vielleicht etwas mehr vorstellen kann, falls man nicht gerade auch einen Resin Drucker zu Hause hat. Los geht’s!
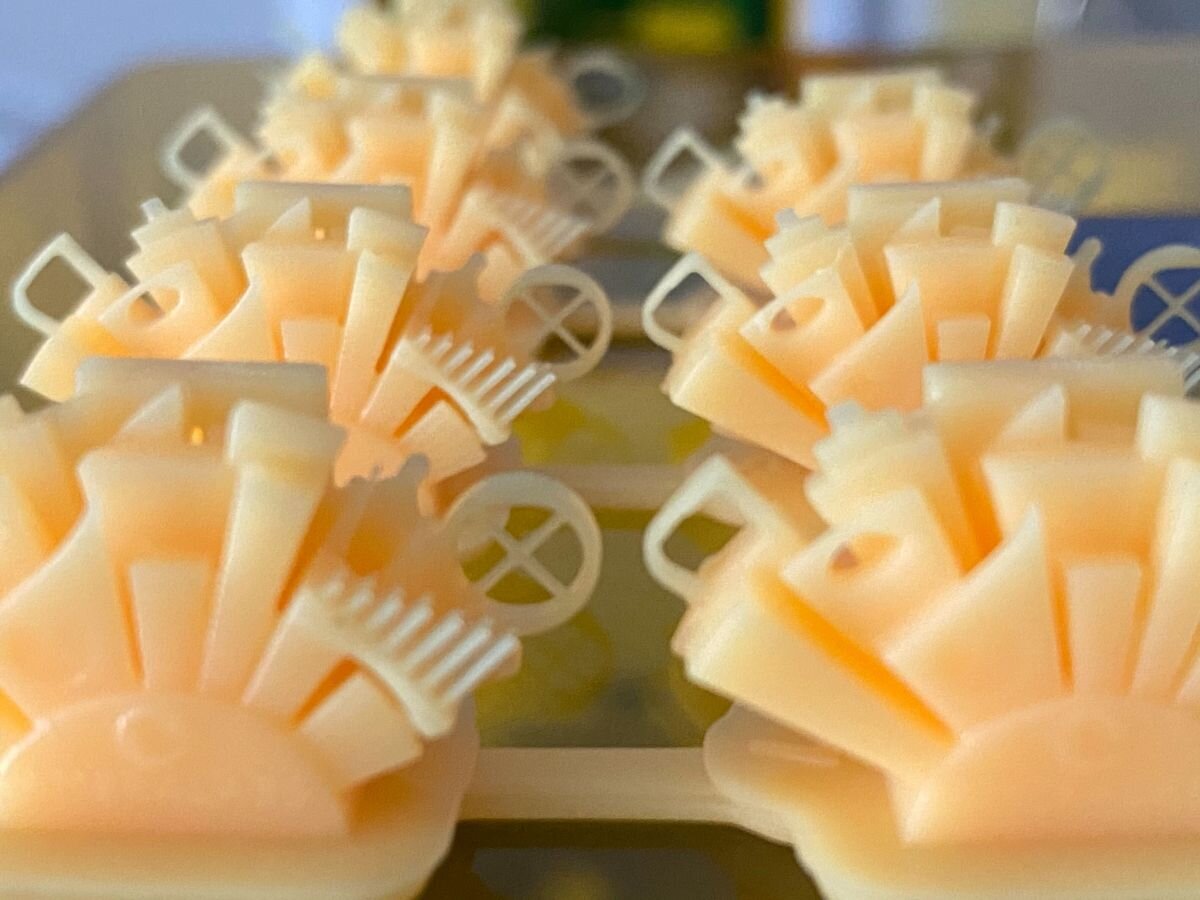
Der 3D-Druck ist eigentlich gar nichts allzu Neues: Bereits in den 70er/80er Jahren wurde FDM (Fused Disposition Modelling) gedruckt. Durch ein Patent geschützt, konnte allerdings nur ein Unternehmen die Technik nutzen, mit Auslaufen des Patentschutzes vor einigen Jahren erlebt der 3D-Druck nun quasi seine Renaissance.
Das Prinzip von FDM ist leicht erklärt: Festes Plastik wird geschmolzen, durch eine Düse gedrückt – welche sich über ein Druckbrett bewegt – und auf die Form zu einem Modell gedruckt. Dabei kann entweder die Düse hoch wandern oder das Brett runter. Hierbei werden sogenannte Supportstrukturen mitgedruckt, die das Modell stützen, wenn es beispielsweise oben breiter ist, sodass ein Teil „in der Luft“ gedruckt werden müsste. Diese werden nachher dann einfach abgeknipst.
Eine andere Art des 3D-Drucks ist Laser-Sintern. Hierbei werden – im Gegensatz zum FDM-Druck – keine Supportstrukturen benötigt. In das Druckbrett wird ein Granulat gestreut. Das kann man sich laut Lennart so vorstellen wie Zucker in einer Zuckerdose. Dort gibt es ja dann auch Körnerschicht um Körnerschicht. Beim Druck ist es nun so, dass die unterste Schicht Granulat entsprechend des Modells mit dem Laser geschmolzen wird, die im Anschluss aushärtet, dann die nächste Schicht usw. Der Rest des Granulats bleibt „krümelig“ und bildet so quasi eine natürliche Supportstruktur, der Druck wird von dem nicht geschmolzenen Granulat getragen.
So! Nach diesem kleinen Exkurs in die Funktionsweise von FDM- und Laser-Sintern kommen wir zum Resin-3D-Druck.
Lange hat Resin funktioniert wie Laser-Sintern: Die im Resin-Drucker genutzte Wanne wird mit dem flüssigen Resin gefüllt (ihr erinnert euch hoffentlich an die lebenswichtige Info aus dem Stream: Giftig!) und von unten mit einem Laser beleuchtet und ausgehärtet. Bei neueren Resin-Druckernwird statt eines Lasers jedoch ein kostengünstiges LCD Panel mit einer starken Lichtquelle dahinter genutzt, um das Resin aushärten zu lassen. So kann eine Schicht „auf einen Schlag“ aushärten und muss nicht mit dem Laser abgefahren werden, was den Druck beschleunigen kann, aber nicht muss. Unabhängig davon, wie viel Struktur gedruckt wird, dauert jede Schicht gleich lang.
Die Auflösung bei Resin ist übrigens deutlich besser als bei FDM-Druckern. Das hier gezeigte Pikachu wurde z. B. mit 0,1 mm Schichthöhe auf einem FDM-Drucker gedruckt und dennoch kann man auf der Oberfläche klar einzelne Schichten erkennen (Foto folgt). Um die Qualität der Oberfläche zu verbessern, könnte man eine kleiner Schichthöhe oder eine Düse mit geringerem Durchmesser als die hier verwendete 0,4mm, verwenden. In der Praxis macht man das aber eigentlich nicht, weil das die Druckzeit, die hier schon bei ca 40h lag nochmal vervielfachen würden. Stattdessen würde man das Objekt nachbearbeiten, z. B. durch Schleifen und Lackieren, um eine schönere Oberfläche zu erhalten. Zum Vergleich haben wir das Modell nochmal mit Resin gedruckt. Hier sieht man direkt die Unterschiede in der Oberflächenqualität. Einzelne Schichten sind kaum noch zu erkennen. Das liegt zum einen an der geringeren Schichthöhe von 0,02mm, als auch an der Tatsache, dass weniger mechanische Ungenauigkeit im System ist.
Bei Resin gibt es keinen Druckkopf, sondern nur eine Achse, die sich lediglich aufwärts- und abwärts bewegen kann. Ein Problem, das jedoch (ausschließlich) bei Resin auftritt, ergibt sich durch die Haftung am Druckbrett, das aus einer leicht angerauten Aluplatte besteht. Man muss immer ein wenig aufpassen, denn im unteren Bereich der Wanne ist wie bei einer Trommel ein Plastikfilm gespannt, der sehr fragil ist, leicht verkratzt und nach einiger Zeit ausgetauscht werden muss. Jedenfalls klebt die Resin-Schicht zunächst zwischen diesem Plastikfilm und der darüber schwebenden Druckplatte. Dadurch, dass der Plastikfilm in der Wanne leicht flexibel ist, die Platte jedoch nicht, wird der Druck beim Anheben des Druckbretts vom Plastikfilm gelöst. Lennart zufolge kann man sich das übrigens so vorstellen, als würde man ein Pflaster von der Haut lösen. Und hierbei ergibt sich folgendes Problem: Die Haftkraft des Druckobjektes am Druckbett muss zu jedem Zeitpunkt größer sein, als die Haftkraft der aktuellen schicht am Film. Wäre umgekehrt die Haftkraft am Film größer, löst sich der Druck vom Brett ab und nicht vom Plastikfilm. Und dann wär‘ halt alles für die Katz. Um das zu erreichen sollte die erste Schicht die gedruckt wird genau so groß sein, wie die größte Schicht des Models. Hierbei unterstützt einen der Slicer, das ist die Software die das 3D-Modell für den Druck vorbereitet, und auf Wunsch auch Hilfsstrukturen wie z.B. Stützen hinzufügen kann.
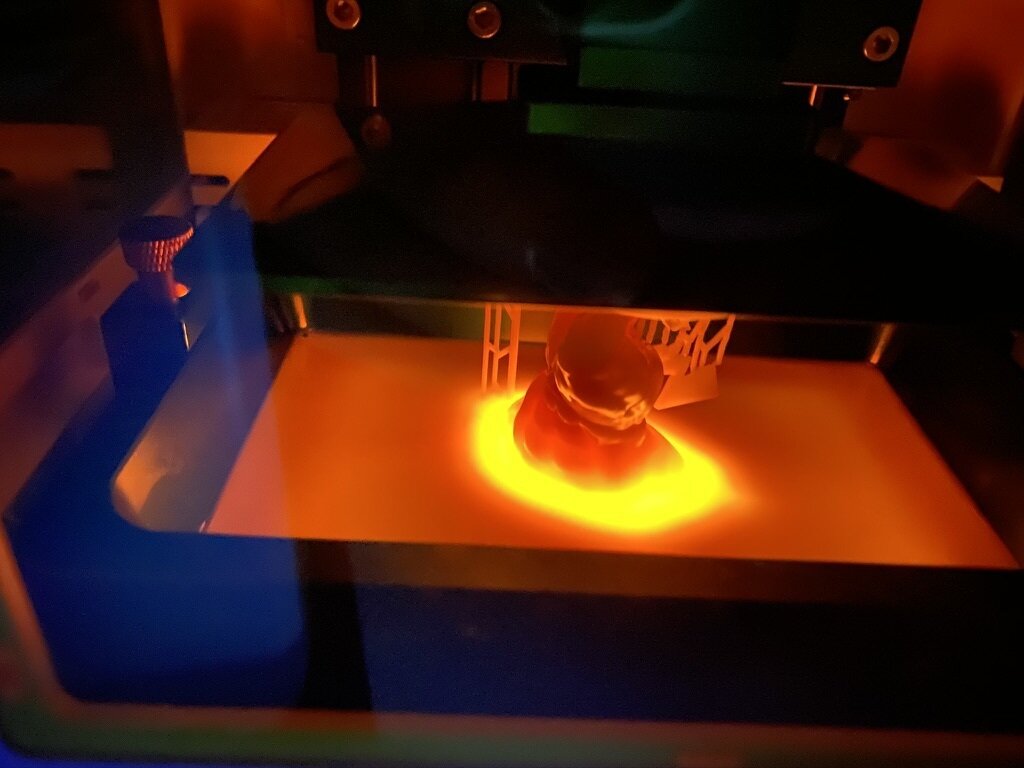
Für alle, die sich (wie ich, als ich Lennart nochmal interviewt habe) fragen, wie so ein Druck jetzt von vorne bis hinten abläuft, folgt hier eine Step-by-Step-Beschreibung:
Am PC:
- 3D Modell selber modellieren, oder aus dem Internet laden
- Aus dem 3D Modell mithilfe eines Slicer Programms eine Datei mit Druckanleitung für den Drucker erstellen.
- Diese Datei auf einem USB-Stick speichern
Danach am Drucker
(Achtung: hierbei Gesichtsmaske und Handschuhe tragen)
- Drucker ggf. reinigen
- Druckwanne mit Resin füllen
- USB-Stick in Drucker stecken
- Auf dem Touchscreen des Drucker das Modell auswählen und auf start drücken
- Warten bis der Druck fertig ist 😉
- Objekt vom Druckbett lösen. Achtung: Das Objekt ist meistens noch weich, kann also leicht beschädigt werden
- Nach dem Druck befinden sich noch giftige Resin-Reste auf der Oberfläche, also das Objekt mit hochprozentigem Isopropanol abwaschen
- Trocknen lassen (ca. 10 min) (Isopropanol lässt das Resin beim aushärten milchig werden)
- Aushärten lassen: In die Sonne, unter eine UV-Lampe mit Drehteller oder Ähnliches stellen
- Drucker reinigen: Küchenkrepp mit Isopropanol, Wanne säubern, Resin-Reste sicher aufbewahren
So. Was Lennart übrigens so toll findet: Klar kann man mit Resin nur kleine Objekte drucken (bei FDM sind der Größe theoretisch keine Grenzen gesetzt; was auch bei Resin ginge, dann aber auch viel teurer und technisch sehr kompliziert wäre), ABER die Bedienung ist im Vergleich zum FDM sehr simpel, sodass dieses Verfahren auch super für Anfänger geeignet ist. Außer der Belichtungszeit der Grundschicht (ihr erinnert euch, damit der Druck am Druckbrett haften bleibt, wenn er kopfüber aus der mit Resin gefüllten Wanne gezogen wird) und die der „normalen“ Schichten sind keine komplizierten Einstellungen am Drucker mehr nötig. Die Belichtungszeit lässt sich übrigens super testen. Auf dem Bild hier seht ihr einen solchen Test, bei dem die gleiche Struktur 8 x mit verschiedenen Belichtungszeiten gedruckt wurde. Prinzipiell wird die Grundschicht lange belichtet, etwa 40-50 Sekunden, damit sie direkt gut aushärtet und haften bleibt, die normalen Schichten meist ca. 4 Sekunden. Dann wird noch das Druckbrett ausgerichtet, welches auf einem Kugelgelenk sitzt, und fertig.
So, das war’s dann auch fürs Erste an dieser Stelle mit 3D-Druck. 😊
Alle Angaben sind wie immer ohne Gewähr.
Tanja & Lennart
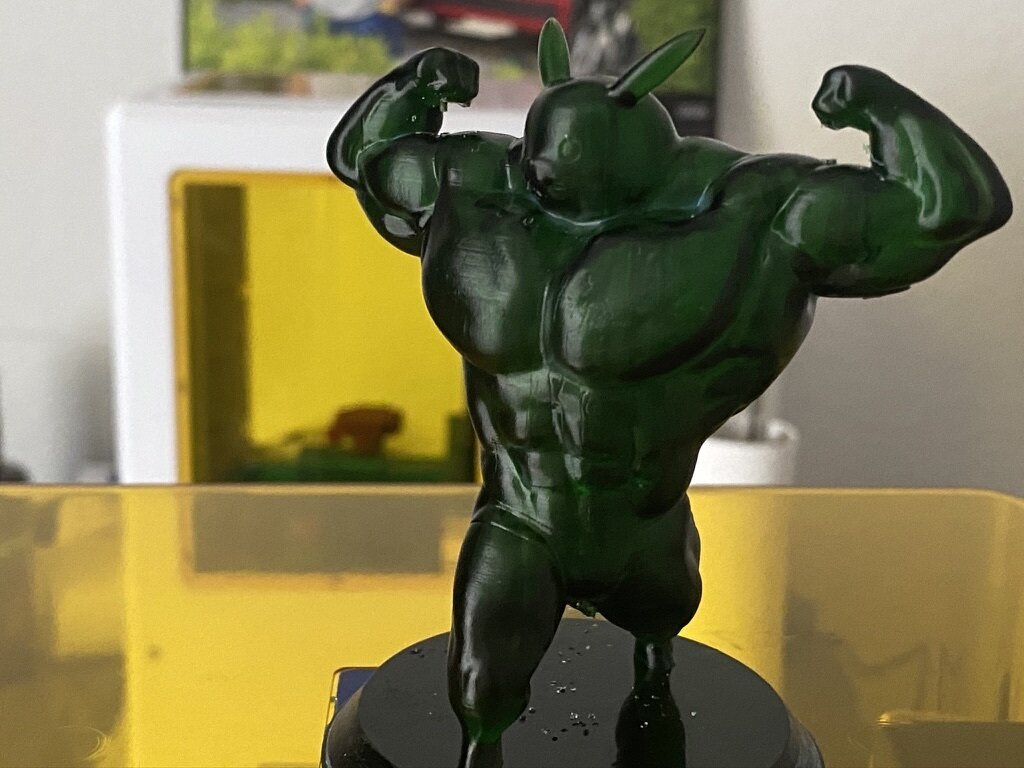